Seamless integration into plant control
In today’s demanding market, a controller must not only deliver maximum performance but also provide transparency. In this respect, the AC 800PEC provides a large range of possibilities. Integrated communication ensures transparent, plant-wide data exchange and control – from overall plant control down to separate processes.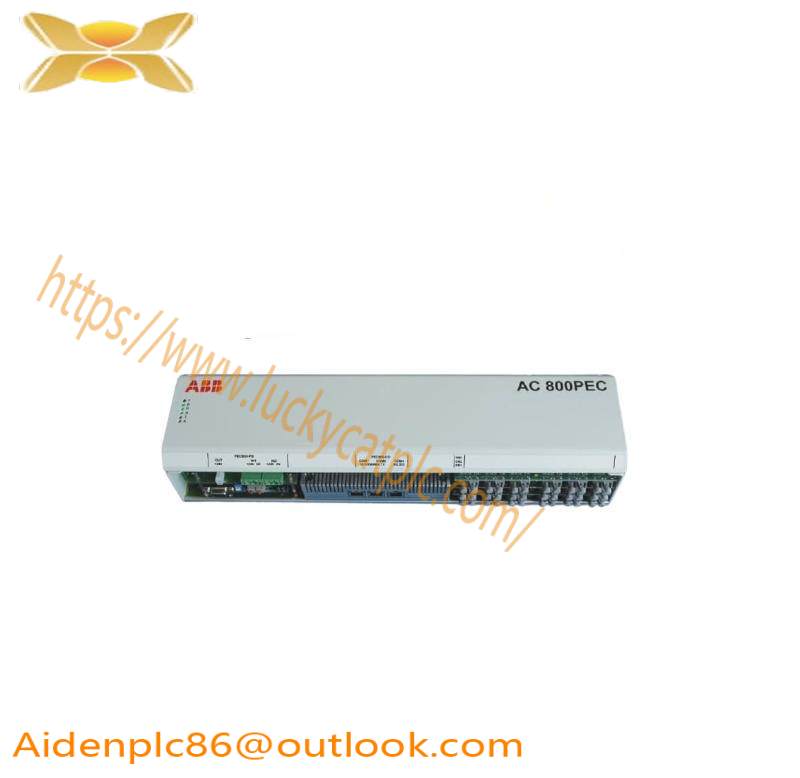
Use of ABB’s System 800xA with the powerful AC 800PEC controller permits uniform automation throughout the plant, seamlessly integrating advanced solutions into the process control system. Strict security procedures and effective firewalls prohibit unauthorized intrusions and ensure permanent system safety.
The AC 800PEC provides connectivity, using either native (built-in) or add-on functionality.
Native (depending on the configuration):
− MMS
− Modbus TCP Slave
− IEC61850
− ABB Powerlink
− ABB Drivebus (DDCS)
− Iba-PDA
− Optical Modulebus (S800)
− CANopen
Add-on:
− Using ABB CEX Modules:
− ABB Drivebus (DDCS)
− Profibus Master DPV1
− Modbus RTU
− S100 I/O
− Masterbus 300
Using Anybus modules:
− CANopen
− ControlNet
− DeviceNet
− Profibus Slave
− Profibus Slave DPV1
− Profibus Master DPV1
− Profinet I/O
− EtherCAT Slave
− Ethernet/IP
Well suited to a harsh environment – the AC 800PEC for traction
Traction with its particularly harsh environmental conditions is one of the most important applications of the AC 800PEC. The controller operates through a wide temperature range (– 40 to + 70 °C), with vibrations according to traction standards. The compact solution is the ideal response to the demands of restricted spaces and allows integration of the processing unit together with all the I/Os in the same compact hardware device.
Top reliability is a must – the AC 800PEC in power generation
Typically, excitation systems are used for generator control in power-plants where high reliability is the No. 1 requirement. Due to the very short process cycles, traditional redundancy concepts are no longer applicable.
The modular architecture of the AC 800PEC not only greatly reduces the complexity of the overall system, but thanks to redundant subsystems also provides increased reliability. In the case of a problem in one subsystem, the main controller switches over to the remaining subsystems, which are scaled in such a way that the overall task can still be fulfilled. Should the main controller fail, a second controller is available in hot-standby.
Precision for optimum quality – the AC 800PEC for industrial processes
The most demanding function in a rolling mill is thickness control. By using the powerful AC 800PEC controller and its ability to implement C-Code beside the standard IEC 61131-3 program level, a new thickness control solution for cold rolling mills has been developed based on an MIMO (MultiInput Multi-Output) control concept. The benefit to the customer is an improvement in thickness deviation by up to 50 percent.
What you simulate is what you implement Straightforward engineering workflow
In the traditional development process, system engineers would define the specifications, which software engineers would then interpret – a time-consuming and error-prone process that also reduced the likelihood that the resultant software would correspond to the original specifications and concept.
The AC 800PEC development workflow uses MathWorks® tools for model-based design as a single development platform for the entire development process.
Simulink® is used to run system simulations. Real-Time Workshop® then automatically generates and downloads controller code from the Simulink® models to the AC 800PEC controller, eliminating the need to translate the models manually into C-code.The use of Real-Time Workshop® allows interactive debugging of the software on the controller. Specification and code are synchronized throughout the development process by using Simulink® models as executable specifications. Parameters can be changed and optimized on the PC, and code can be generated automatically from the models and then transferred to the controller directly via an Ethernet connection.
Related recommendations:
3BHE020570R1022 PPD114 B1022
3BHE014135R0011 UAD149 A00-0-11
PP D113 3BHE023784R2030
AC 800PEC 3BHE025541R0101
AC800F PM803F Base
HF HF2211A
3BHE023784R1023
PP D113 PPD113 3BHE023784R2630 B01-26-111000
PPD113 3BHE023584R2634
3BHE020570R1022 PPD114 B1022
3BHE020455R0001 PPD103 B01
PPD113B03 – 3BHE023584R2365
3BHE041576R3011 PPD517 A3011
PPD113B01 3BHE023784R1010
PPD114B1022 – 3BHE020570R1022
PPD104 3BHE017400R0101
more……